IIoT and AI for predictive maintenance
How many times have your manufacturing process get interrupted due to the machine down time?
Imagine harnessing the power of AIoT for predictive maintenance.
* AIoT & Predictive Maintenance
* Preventive maintenance vs predictive maintenance – which is more efficient?
* IoT Device that helps in gathering crucial data for predictive maintenance
That was the title of the #11 ” JOM! lets Sembang AIoT”.
During the live sharing on the Predictive Maintenance with AI and Industrial IoT, Tan Kien Leong has started with the brief introduction of how the maintenance process was carried out in the past and what are the limitation with the process of maintenance being performed in the old days. One of the recently practiced preventive maintenance is used to make a comparison to the newly introduced Prediction Maintenance.
Preventive maintenance (PM) and predictive maintenance (PdM) are both proactive approaches to maintaining equipment and systems, but they differ in methodology, technology, and application. Here are the main differences between the two:
- Definition:
- Preventive Maintenance (PM): Maintenance activities are performed at predetermined intervals or according to prescribed criteria, regardless of the actual condition of the equipment. It’s based on time or usage (e.g., every 10,000 miles or 1,000 operating hours).
- Predictive Maintenance (PdM): Maintenance is performed based on the actual condition of the equipment, as determined by monitoring and analyzing data from sensors, diagnostics, and analytics tools. The goal is to predict when a failure might occur and perform maintenance just in time to avoid unplanned downtime.
- Methodology:
- PM: Often follows manufacturer’s recommendations, historical data, or industry best practices.
- PdM: Relies on real-time data and condition-monitoring tools, such as vibration analysis, infrared thermography, ultrasound, and oil analysis.
- Technology Utilization:
- PM: Typically uses basic scheduling tools or CMMS (Computerized Maintenance Management Systems) to keep track of maintenance tasks.
- PdM: Utilizes advanced technologies, including IoT sensors, machine learning algorithms, and data analytics to predict equipment failures.
- Cost:
- PM: Can sometimes lead to over-maintenance, resulting in unnecessary costs and potential wastage of parts and labor.
- PdM: Often results in cost savings by preventing unexpected breakdowns and minimizing maintenance activities to only when necessary.
- Waste:
- PM: There’s potential waste as parts might be replaced or maintained even if they’re still in good condition.
- PdM: Minimizes waste because components are only serviced or replaced when their condition indicates a need.
- Downtime:
- PM: Maintenance shutdowns are scheduled, but there’s still a risk of unexpected failures between scheduled maintenance activities.
- PdM: Reduces unplanned downtime since maintenance is performed when there’s a clear indication of deterioration.
- Implementation Complexity:
- PM: Easier to implement, as it’s based on set schedules or intervals.
- PdM: More complex due to the need for advanced tools, sensors, and data analysis capabilities.
- Flexibility:
- PM: Fixed schedule, less flexibility.
- PdM: Highly flexible and adjusts based on actual equipment condition.
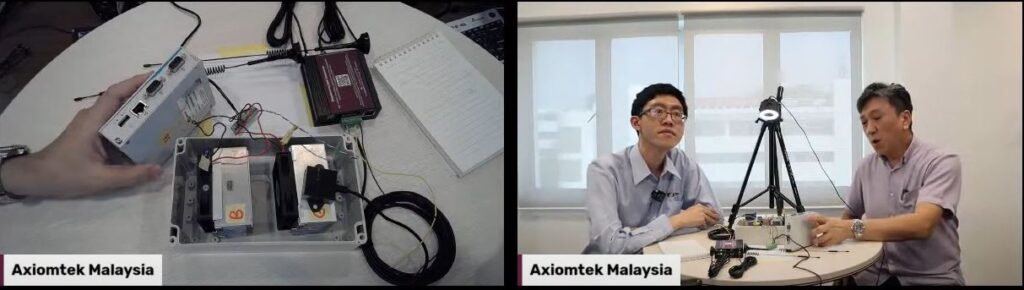
In the demonstration, the Vibrational data from two rotating fan were used as a source of vibration signal being captured. The data is collected via the 4G router gateway ( AEC310) and optional we can use Axiomtek IIoT edge gateway.
Three-axis vibration measurement
Frequency range: 10 Hz to 1K Hz
Amplitude range: ±8g
Data Format:
-Acceleration(mg): RMS,
Maximum, P-P
-Velocity(mm/s): RMS
-Top 10 spectrum values(Amplitude/Frequency)
To Watch the live session, please click the link below:-